はじめに:電動化の波に乗り遅れた日本、逆転の切り札
自動車産業の電動化において、日本は厳しい現実に直面している。多くの自動車メーカーが注目しているのが全固体電池だ。リチウムイオン電池の温度変化に弱い、発火リスクといった弱点を克服できることもあり、各国の自動車メーカーや電子部品メーカーがEV搭載バッテリーの実用化に向け、熾烈な開発競争を繰り広げている状況下で、日本は欧州各国のEV推進に大きく後れを取っているのが現状だ。
しかし、まさにこの危機的状況こそが、日本の技術力を結集した大逆転劇の序章となろうとしている。世界最大級の自動車メーカー・トヨタ自動車と、石油精製技術で培った独自の材料開発力を持つ出光興産が手を組み、「全固体電池」という次世代技術によって、再び世界の自動車産業をリードしようとしているのだ。
この記事では、両社が進める全固体電池の実用化プロジェクトの全貌を、技術的詳細から実用化スケジュール、そして私たちの日常生活に与える革命的な変化まで、他では得られない深い洞察とともに解説していく。
第1章:全固体電池とは何か? – 技術革新の核心を理解する
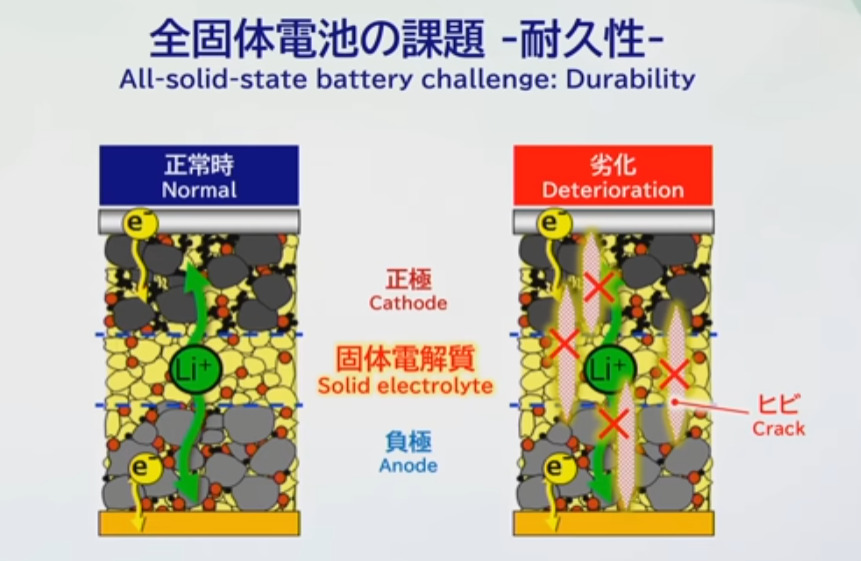
1.1 従来のリチウムイオン電池の限界
現在のEVに搭載されているリチウムイオン電池は、確かに画期的な技術であり、私たちのモバイル社会を支えてきた。しかし、EVという大型用途に適用すると、その限界が浮き彫りになる。
リチウムイオン電池は今や私たちの暮らしに欠かせないものとなりましたが、安全面では課題もあります。長期間使用を続け劣化が進むと、リチウムが漏れたり、ガスが発生して膨張したりする危険性があるのです。また決して衝撃に強いとはいえず、気温差などにも注意が必要で、保管場所には気をつかわなければなりません。
さらに、EVの実用性を大きく左右する充電時間の長さ、限られた航続距離、高温下での性能低下など、従来技術では解決困難な課題が山積している。これらの課題こそが、EVの普及を阻む大きな壁となっているのだ。
1.2 全固体電池の革命的な構造
大きな違いは、リチウムイオン電池では電解質が液体、全固体電池では固体という点です。固体の電解質を用いることで、液体リチウムイオン電池が抱えていた電解質の蒸発や液漏れのリスクを解消できます。
この一見シンプルな違いが、実は電池技術における革命的な転換点となる。全固体電池の構造を詳しく見てみよう。
従来のリチウムイオン電池の構造:
- 正極(リチウム化合物)
- 液体電解質(有機溶媒にリチウム塩を溶かした溶液)
- セパレーター(正極と負極を物理的に分離する多孔質膜)
- 負極(黒鉛など)
全固体電池の構造:
- 正極(リチウム化合物)
- 固体電解質(セラミックスや硫化物系材料)
- 負極(リチウム金属やシリコン系材料)
電解液を採用した場合、電気を通すイオンが液体の中を伝わりますが、全固体電池では、固体の中をイオンが移動します。つまり全固体電池の場合、電池からの液漏れを気にする必要はありません。また全固体電池では、リチウムイオン電池に必要なプラス側とマイナス側を隔てるセパレーターも要らないという特徴があります。
1.3 固体電解質の種類と特性
全固体電池は、製造方法によって大きく「バルク型」と「薄膜型」に分類され、それぞれ蓄えられるエネルギーの量が異なります。
バルク型全固体電池:
- 高容量・高エネルギー密度を実現
- EV用途に最適
- 製造プロセスが複雑だが、大容量化が可能
薄膜型全固体電池:
- 小型・薄型化に適している
- ウェアラブル機器や小型電子機器に適用
- 製造が比較的容易だが、容量は限定的
固体電解質の材料には、主に以下の種類がある:
- 酸化物系固体電解質
- 化学的安定性が高い
- 大気中での取り扱いが容易
- イオン伝導度がやや低い
- 硫化物系固体電解質
- 極めて高いイオン伝導度
- 柔軟性があり、電極との密着性が良好
- 大気中で不安定(湿気に弱い)
トヨタと出光が選択したのは、この硫化物系固体電解質だ。その理由と独自技術については後述するが、この選択こそが両社の戦略の核心となっている。
第2章:トヨタ×出光協業の全貌 – なぜこの組み合わせなのか
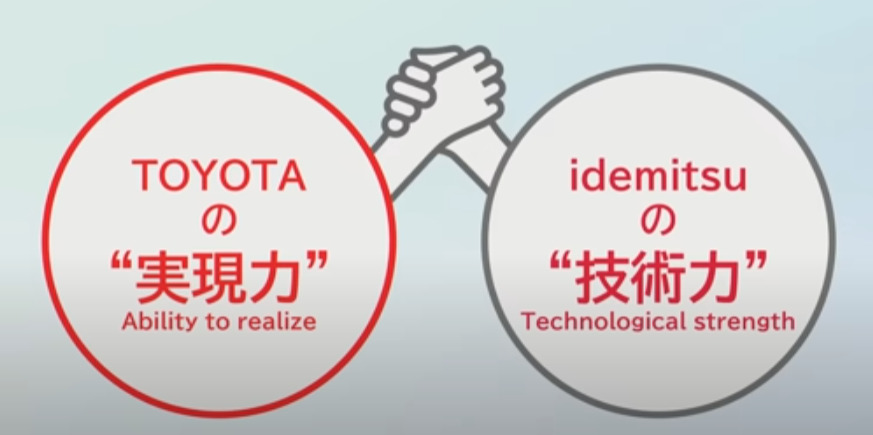
2.1 異業種連携の戦略的意義
出光による量産実証(パイロット)装置の製作・着工・立ち上げを通じた、硫化物固体電解質の製造と量産化を推進しますという発表は、単なる業務提携を超えた、日本の産業構造を変える可能性を秘めている。
自動車産業と石油産業。一見相反するように見える両者の連携には、深い戦略的意図がある。
トヨタの強み:
- 世界最高水準の自動車製造技術
- ハイブリッド技術で培った電動化のノウハウ
- グローバルな販売・サービスネットワーク
- 品質管理と量産化技術
出光の強み:
- 石油精製プロセスで培った化学技術
- 硫黄成分を活用した独自の材料開発力
- 大規模プラント運営のノウハウ
- エネルギー産業としてのインフラ基盤
2.2 出光の「硫化物系固体電解質」への特化戦略
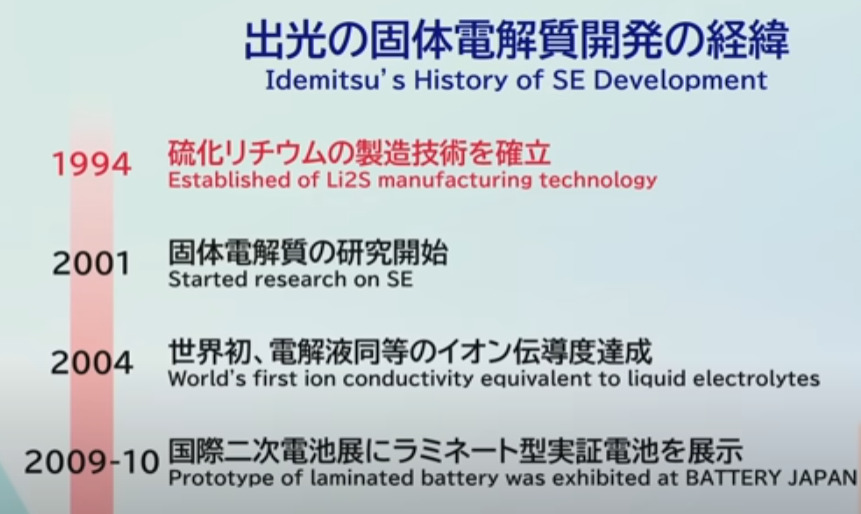
出光が、固体電解質の原料となる硫化リチウムの製造技術を確立したのは1994年という事実は、この協業の成功確率を大きく高める要因となっている。
出光の戦略の独創性は、石油精製の副産物である硫黄を活用した点にある。従来は処理に困る副産物だった硫黄が、次世代電池の核心材料となる硫化物系固体電解質の原料として生まれ変わるのだ。
出光の電解質は電池性能のカギとなるイオンの移動が速く、電極と密着する柔らかさが特徴。この「柔らかさ」こそが、全固体電池の実用化における最大の課題を解決する鍵となる。
2.3 実用化に向けた具体的スケジュール
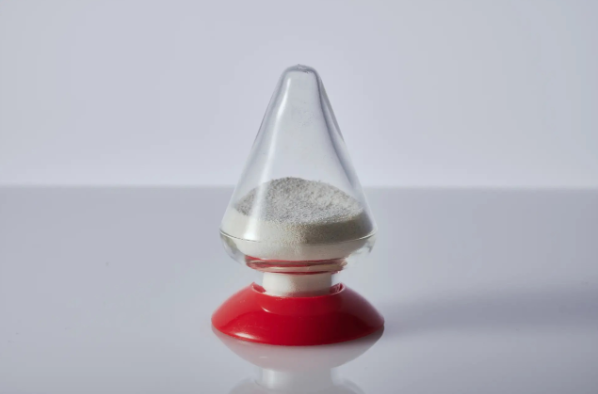
出光興産は10月28日、2027~2028年の全固体リチウムイオン二次電池の実用化を目指し、固体電解質の大型パイロット装置の基本設計を開始した、と発表した。生産能力は年間数百トンを予定しており、世界でもトップクラスの規模となる。
このスケジュールの具体性と実現可能性は、他の競合企業とは一線を画している。
2024年: 大型パイロット装置の基本設計開始 2025年: 最終投資決定(FID) 2027年: パイロット装置完工、量産技術確立 2027-2028年: 全固体電池搭載EV市場投入
2025年2月には、固体電解質の中間材料である硫化リチウムの大型製造装置を出光の千葉事業所(千葉県市原市)に建設すると発表した。2027年6月の完工を目指すという詳細な計画は、単なる研究開発プロジェクトではなく、確実な事業化を見据えた戦略的投資であることを示している。
第3章:全固体電池がもたらす性能革命
3.1 充電時間の劇的短縮 – 10分以下の超高速充電
現在のEVの最大の弱点である充電時間。家庭用の普通充電では一晩、急速充電でも30分から1時間を要するのが現状だ。この常識を全固体電池は根底から覆す。
超高速充電を可能にする技術的要因:
- 高いイオン伝導度
- 安全性や信頼性の観点から、固体電解質を用いた全固体電池は電池の理想形と考えられていますが、同時に固体であるがゆえに、イオンを高速で伝導させることが難しく、それが本格的な普及に向けた壁となっています
- しかし、硫化物系固体電解質は液体電解質に匹敵する高いイオン伝導度を実現
- 電気分解反応の抑制
- 全固体電池の固体電解質は電気分解反応を受け難い為、従来のリチウムイオン二次電池では4V程度が限界だった充電電圧を大幅に引上げる事が可能となる
- 高電圧充電により、より短時間での充電が可能
- 熱管理の向上
- 固体電解質の耐熱性の高さも急速充電時の稼働温度範囲を拡大し、安全な高速充電を実現
3.2 航続距離の飛躍的向上 – 1000km超の長距離走行
現在の市販EVの航続距離は、リーフの約400km、テスラModel Sの約600kmが上限に近い。全固体電池はこの数値を1000km以上に引き上げる。
長距離走行を実現する技術的要因:
- 高エネルギー密度
- 同じ体積・重量で、より多くのエネルギーを蓄積可能
- 車両重量の増加を抑制しながら大容量化
- 劣化特性の改善
- 全固体電池は固体の電解質であるため副反応が起こりにくく、液体のリチウムイオン電池に比べて劣化しにくい特性がある
- 長期間にわたって高い性能を維持
- 温度特性の向上
- 低温から高温まで安定した性能
- 季節や気候による航続距離の変動を最小化
3.3 安全性の飛躍的向上 – 発火・爆発リスクの根本的解決
EVの普及を阻む大きな要因の一つが、リチウムイオン電池の安全性への懸念だ。全固体電池は、この課題を根本的に解決する。
安全性向上の技術的根拠:
- 不燃性
- 液体電解質(有機溶媒)がないため、発火・爆発のリスクが大幅に低減
- 高温になっても熱暴走を起こしにくい
- 機械的強度
- 固体構造により、外部からの衝撃に対する耐性が向上
- 変形や破損時の安全性が大幅に改善
- 化学的安定性
- 電解質の漏洩がない
- 長期保存時の安全性も確保
第4章:技術的課題とその解決策
4.1 界面抵抗問題への取り組み
全固体電池の最大の技術的課題は、固体電解質と電極材料の界面における抵抗の増大だ。この課題に対し、トヨタと出光は独自のアプローチで解決を図っている。
界面抵抗が生じる原因:
- 固体同士の接触では、原子レベルでの密着が困難
- 充放電の繰り返しにより、界面に微細な隙間が発生
- イオンの移動経路が制限され、抵抗が増大
出光の硫化物系固体電解質による解決策:
- 材料の「柔らかさ」により、電極との密着性を向上
- 充放電による体積変化に追従し、界面を維持
- 製造プロセスでの圧力制御により、初期界面を最適化
4.2 製造プロセスの確立
全固体電池の量産には、従来のリチウムイオン電池とは全く異なる製造プロセスが必要となる。
主な製造工程:
- 固体電解質の合成・加工
- 電極材料との複合化
- 積層・圧着プロセス
- 封止・パッケージング
トヨタの製造技術と出光の材料技術の融合により、これらの工程を効率的に実現する独自のプロセスが開発されている。
4.3 コスト競争力の確保
新技術の普及には、既存技術との価格競争力が不可欠だ。固体電解質の量産技術を開発し、自動車メーカーや電池メーカーのニーズに応える方針だという出光の戦略は、コスト削減への強い意志を示している。
コスト削減戦略:
- 石油精製の副産物を活用した原料コスト削減
- スケールメリットを活かした大量生産
- 製造プロセスの効率化・自動化
第5章:実用化後の社会変革シナリオ
5.1 自動車産業の構造変化
全固体電池の実用化は、自動車産業の競争構造を根本的に変える可能性がある。
短期的影響(2027-2030年):
- トヨタの競争優位性確立
- 他メーカーの追随と技術開発競争激化
- EV市場の急速な拡大
中長期的影響(2030年以降):
- ガソリン車からの完全移行加速
- 自動車の用途・デザインの多様化
- 新たなモビリティサービスの創出
5.2 エネルギー産業への波及効果
電力網への影響:
- 超高速充電インフラの整備需要
- 電力需要の平準化(長航続距離により充電頻度減少)
- 再生可能エネルギーとの連携強化
石油産業の転換:
- 出光のような石油会社の新事業領域拡大
- 既存インフラの活用による競争優位性
5.3 ライフスタイルの変化
個人の移動スタイル:
- 長距離移動への不安解消
- 充電計画の簡素化
- 車両デザインの自由度拡大
都市計画・インフラ:
- 充電インフラの最適配置
- 駐車場・商業施設の設計変更
- スマートシティ構想との連携
第6章:国際競争における日本の戦略的優位性
6.1 特許戦略と技術的優位性
日本の全固体電池技術における特許保有状況は、国際競争において重要な優位性を提供している。トヨタと出光は、硫化物系固体電解質に関する基本特許を多数保有しており、これが競合他社に対する大きなアドバンテージとなっている。
日本の技術的優位性:
- 基礎研究からの長期的取り組み
- 材料科学における深い知見
- 製造技術の高度化
6.2 中国・韓国勢との競争
中国の動向:
- 政府主導の大規模投資
- 既存リチウムイオン電池での圧倒的シェア
- 全固体電池への参入加速
韓国の動向:
- サムスン、LGエナジーソリューションの技術開発
- 酸化物系固体電解質への注力
- 製造技術の高度化
日本の対抗戦略:
- 硫化物系での技術的優位性確保
- 量産技術の早期確立
- グローバルパートナーシップの構築
6.3 欧米市場での展開戦略
北米市場:
- テスラとの競争
- 米国政府のEV推進政策活用
- 現地生産拠点の検討
欧州市場:
- 厳格な環境規制への対応
- 欧州自動車メーカーとの連携
- 技術ライセンス戦略
第7章:技術開発の最前線 – 研究開発の詳細
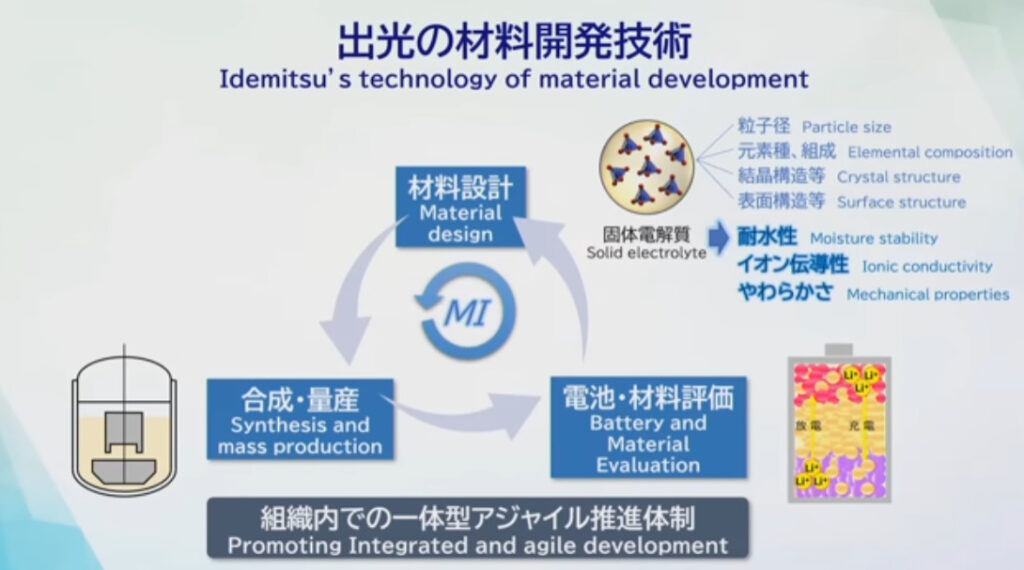
7.1 硫化物系固体電解質の化学的特性
出光が開発する硫化物系固体電解質の化学組成と特性について、より詳細に解説する。
基本組成:
- Li₂S(硫化リチウム)をベースとした複合材料
- P₂S₅(五硫化リン)との反応による高イオン伝導相の形成
- 添加元素による特性制御
イオン伝導メカニズム:
- リチウムイオンの拡散経路の最適化
- 結晶構造と非晶質相の制御
- 界面での電荷移動反応の促進
製造プロセス:
- メカニカルミリング法による微細化
- 熱処理による結晶化制御
- 成型・焼結プロセスの最適化
7.2 電極材料との相互作用
正極材料との界面:
- LiCoO₂、LiNi₀.₈Co₀.₁Mn₀.₁O₂等との相性
- 界面抵抗の低減技術
- 長期安定性の確保
負極材料との界面:
- リチウム金属負極の採用
- デンドライト成長の抑制
- 界面安定化層の形成
7.3 セル設計とパッケージング技術
積層構造の最適化:
- 電極厚さと固体電解質厚さのバランス
- 集電体の設計
- 熱管理システムとの統合
封止技術:
- 大気からの保護
- 機械的応力の緩和
- 長期信頼性の確保
第8章:量産化への道筋
8.1 パイロットプラントの詳細
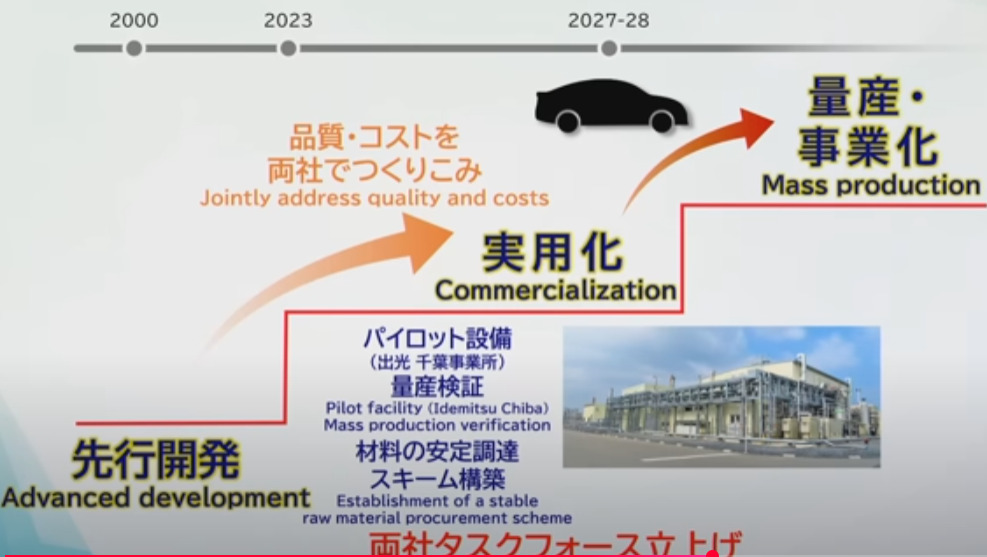
出光興産は、2027~2028年の全固体電池(全固体リチウムイオン二次電池)の実用化を目標に、全固体電池の材料となる固体電解質の大型パイロット装置の基本設計を2024年10月に開始したと発表した。
パイロットプラントの仕様:
- 生産能力:年間数百トン
- 設置場所:千葉事業所
- 投資規模:数百億円規模(推定)
- 完工予定:2027年
技術検証項目:
- 連続生産プロセスの確立
- 品質管理システムの構築
- コスト削減技術の実証
- 環境負荷の最小化
8.2 品質管理と標準化
品質管理システム:
- 原料から最終製品までの一貫管理
- リアルタイム品質監視
- 不良品の早期検出と排除
標準化戦略:
- 国際標準規格への準拠
- 自社規格の業界標準化推進
- 認証取得とブランド価値向上
8.3 サプライチェーンの構築
原料調達戦略:
- 硫黄の安定調達(石油精製副産物活用)
- リチウム原料の多様化
- 戦略的在庫の確保
製造拠点展開:
- 国内拠点の拡充
- 海外展開の検討
- 災害リスクの分散
第9章:市場への影響予測
9.1 EV市場の成長予測
全固体電池の実用化がEV市場に与える影響を定量的に予測する。
2025-2030年の市場予測:
- 全固体電池搭載EV:年間100万台(2030年)
- 市場規模:5兆円(2030年)
- 日本メーカーのシェア:30-40%
用途別市場:
- 乗用車:70%
- 商用車:20%
- 特殊車両:10%
9.2 既存技術への影響
リチウムイオン電池市場:
- 段階的な置き換え
- 用途の棲み分け
- 価格競争の激化
燃料電池車への影響:
- 用途特性の再整理
- 長距離・大型車両への特化
- 水素インフラとの関係
9.3 新たなビジネスモデル
バッテリー・アズ・ア・サービス:
- 電池のリース・サブスクリプション
- 性能保証サービス
- リサイクル・循環経済
エネルギーマネジメント:
- V2G(Vehicle to Grid)サービス
- 再生可能エネルギーとの連携
- スマートグリッド統合
第10章:環境・社会への貢献
10.1 カーボンニュートラルへの貢献
CO₂削減効果:
- 製造段階でのCO₂削減
- 使用段階での排出ゼロ
- リサイクルによる資源循環
ライフサイクル評価:
- 原料採掘から廃棄まで
- 他技術との比較評価
- 継続的改善
10.2 資源循環の推進
材料リサイクル:
- リチウム、硫黄の回収
- 希少金属の有効活用
- 廃棄物の最小化
設計思想:
- サーキュラーエコノミー
- 分解・回収容易性
- 長寿命設計
10.3 社会インフラへの貢献
災害時の活用:
- 非常用電源としての活用
- 避難所への電力供給
- 災害復旧支援
地域活性化:
- 製造拠点の雇用創出
- 関連産業の集積
- 技術者育成
第11章:課題と今後の展望
11.1 技術的課題の継続的解決
短期的課題(2025-2027年):
- 量産プロセスの確立
- コスト競争力の確保
- 品質安定性の向上
中長期的課題(2027年以降):
- さらなる性能向上
- 新材料の開発
- 次世代技術への展開
11.2 市場受容性の向上
消費者啓発:
- 技術的優位性の訴求
- 安全性への理解促進
- 使い勝手の改善
インフラ整備:
- 超高速充電器の普及
- 充電ネットワークの拡充
- メンテナンス体制の構築
11.3 国際競争力の維持・向上
技術開発の継続:
- 基礎研究への投資
- 人材育成・確保
- 産学連携の推進
知的財産戦略:
- 特許ポートフォリオの強化
- 標準化活動への参画
- ライセンス戦略の最適化
結論:日本の技術力が切り開く新たな未来
トヨタと出光興産による全固体電池の実用化プロジェクトは、単なる新技術の開発を超えた、日本の産業競争力復活への切り札となる可能性を秘めている。
石油精製で培った出光の素材技術という異色の強みと、自動車製造の匠たるトヨタの技術が融合し、「実現力」を持って世界をリードする。この日本発のイノベーションは、以下の点で画期的な意義を持つ:
技術的革新の意義:
- 従来不可能とされた10分以下の超高速充電
- 1000km超の長距離走行能力
- 根本的な安全性の向上
- 設計自由度の飛躍的拡大
産業構造への影響:
- 自動車産業の競争構造の変革
- エネルギー産業の新たな展開
- 日本の製造業復権への道筋
- グローバルサプライチェーンの再構築
社会的インパクト:
- カーボンニュートラル社会の実現加速
- 移動の自由度向上とライフスタイル変化
- 地方創生と産業集積の新たな可能性
- 災害時の社会インフラとしての役割
現在、両社から数十名規模のタスクフォースが立ち上がり、2027-2028年の実用化に向けた具体的な取り組みが加速している。この挑戦が成功すれば、日本は再び世界の自動車産業をリードし、カーボンニュートラル社会の実現において中心的役割を果たすことになるだろう。
全固体電池が切り開く未来は、単なる技術的進歩を超えて、私たちの生活様式、社会構造、そして地球環境との関係を根本的に変える可能性を秘めている。トヨタと出光が仕掛けるこの壮大な挑戦の行方を、私たちは注目し続けていく必要がある。
この記事は、公開されている情報と技術資料に基づいて作成されており、継続的に更新される予定です。全固体電池技術の最新動向については、各社の公式発表をご確認ください。